3D Printed Oil Bottle Concept Prototype
- Team Positron
- Apr 28, 2021
- 2 min read

When working at a 3D Printing service bureau, you come across a lot of immediate requirements for form & fitment testing, concept & visualization prototype NPD's, etc. Recently one of our customer who is leading Poly-mold house bottle manufacturer in Pune, came with requirement of Oil bottle prototype which was 400mm in height and 138mm in diameter and wanted it on the same day as they were having product presentation to the end customer team a day after where they are expecting final go ahead for the blow mold and manufacturing.
We suggested them immediate solution that we can split the bottle in 3-4 pieces and we can print it on multiple printers and can join after printing. But client wanted part in single piece without any joint as they wanted to check the amount of oil it takes.
We explored multiple options like SLA, MJF, SLS but as timeline was very crucial and customer wanted part in the same day.

We started evaluating other options to fulfil the requirement, started with build time and orientation. With 250 microns layer height on our FDM printer it was showing around 45 hrs. of build time. So we started increasing layer height and evaluate the same but still the reducing print time was huge challenge.
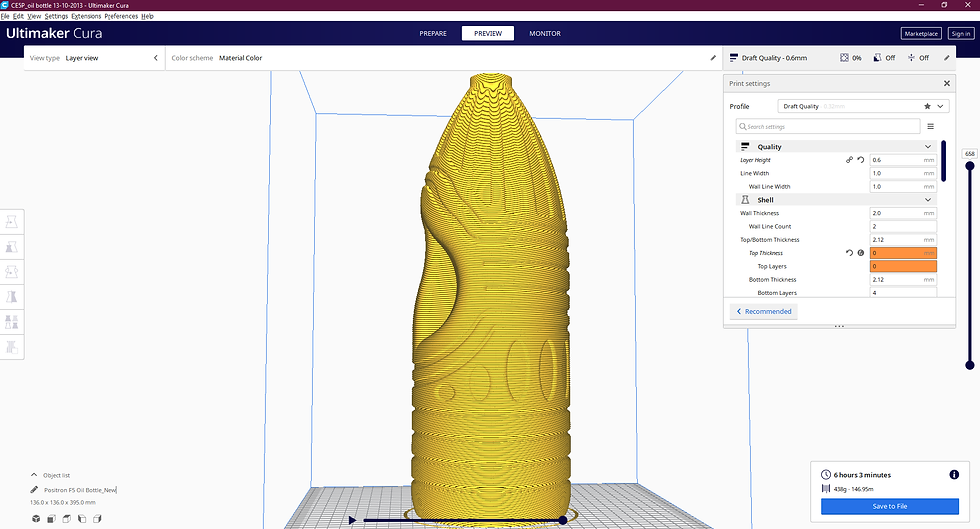
Then we thought to replace 0.4 mm dia nozzle with 1.0 mm dia nozzle. Surprisingly we got good results in reducing print time. So further we increased layer height to 600 microns and kept 2 wall layers i.e. 2.0mm wall thickness. With 1.00 mm nozzle dia we achieved around 73-75 cc/hr material deposition rate which is very high. With these setting we were able to print the part in 6 hrs 3 min and we handed over the same to the client in end of the day.
The observed layer deposition and finish was also acceptable and it was uniform over the height of the bottle. With 1.0mm nozzle in FDM and 600 microns layer height the strength was superb as compared to the standard 0.4 mm nozzle printing. Further we applied resin coat on the bottle for making it fluid-tight.
The client was satisfied with the solution and part quality.
We wanted this project badly in this pandemic situation to boost our business, the product presentation and design approval meeting with end client team was on next day, we were confused and prototype was not yet ready, we went to positron team for the prototype, we know getting this huge part on the same day was challenging, but Positron team amazed us with the solution, service and part quality. They used bigger size nozzle and printed part in 6 hrs in FDM. Much appreciable. They took complications of manufacturing, helping our team to focus on end goal.
-Project Manager, Design Team
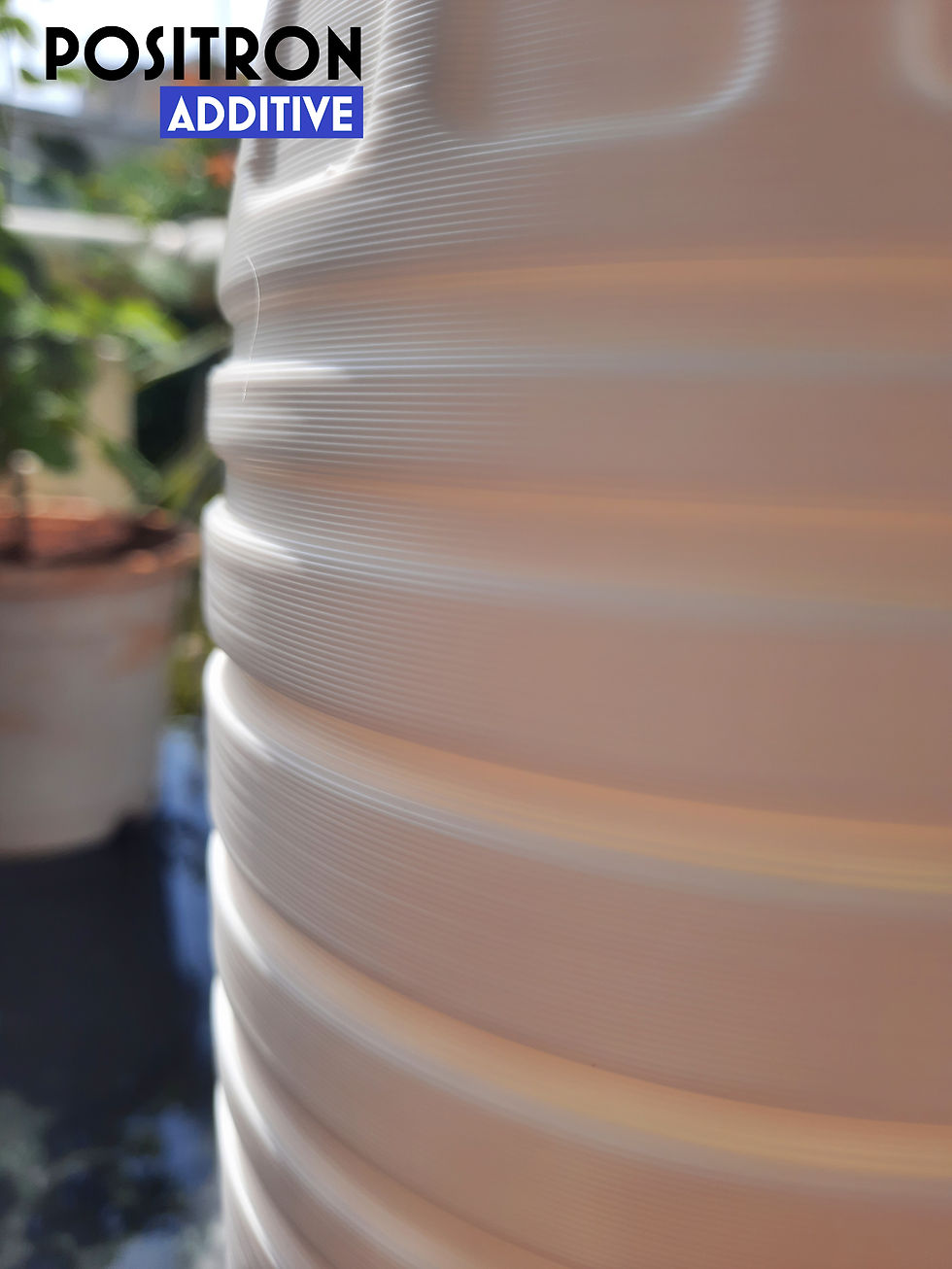


For any help & assistance reach us, Email: proto@positronadditive.com Mobile: 09307992744
Comments